差速流化床锅炉与普通流化床的区别和运行调节应对措施
我们建湖热电公司目前运行的常见两种流化床锅炉,有高倍率循环流化床锅炉和高低差速床锅炉。
一、高倍率流化床锅炉的优势
高倍率循环流化床锅炉是借助于其高循环倍率的特点,使燃料能在炉膛内多次燃烧,同时炉膛内传热主要是靠高温物料与水冷壁碰撞实现的,这就使它具备了以下优点:
高效的高温烟气分离装置(旋风分离器,回料立柱,返料阀组成的回料系统),最终煤的燃烧效率较高。与煤粉炉及链条炉相比,煤种的适应性广,对低热值3500Kcal/Kg以上的煤均能有效使用。
二、高倍率流化床锅炉的劣势
由于炉膛内传热主要是靠大量的高温物料与水冷壁碰撞实现的,这就造成了水冷壁受热面的整体磨损严重;高浓度的烟气中物料携带量以及高温分离的影响,导致烟气分离器的磨损严重;
燃用热值在3500Kcal/Kg以下的太低热值燃料时,出力较难保证。
锅炉出力须靠烟气中的物料浓度来保证,当返料器系统出现故障,返料不通畅时,将对锅炉出力产生直接影响;
由于采用了较高的循环流速,燃料在炉膛内的一次通过时间短,造成飞灰中含炭量偏高;
较高的厂用电率。
三、差速流化床锅炉的优势
由于密相区埋管的存在,工作稳定可靠,保留了埋管结构,增加受热面,保证了锅炉对燃料的适应性广及出力足等特点,同时又解决了埋管易磨损的问题;
锅炉出力稳定,与烟气携带量及返料情况好坏关联度小;
无分离器,结构简单;
独特的锅炉内循环及外循环结合,使锅炉燃烧效率大大提高,经济性能好;
采用分床燃烧技术
燃烧系统温度较低,环保性强等特点。
四、高低差速床的结构及工作原理
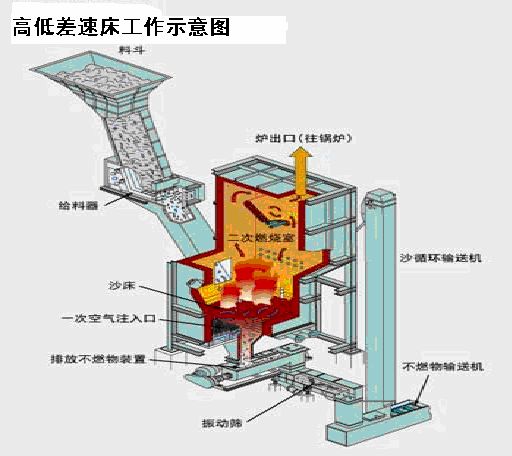
五、高低差速床的工作原理
燃料颗粒的自选过程以及高速床和低速床不同风速的实现。由炉膛两侧给入锅炉主床,床料颗粒在主床上沸腾燃烧,同时其中的大颗粒开始向下沉,在较低的位置处沸腾燃烧,小颗粒则溢于表面。由于高速床与低速床之间有一个高度差,此高度差保证了大颗粒不会被带入低速床,只需较低的流化风速即可实现低速床的流化,而主床仍采用常规流化床的流化风速以保证大颗粒的流化燃烧。特有的炉内循环形成机理,由于高速床与低速床之间不同的流化风速,溢流于高速床上表面的细颗粒在主床较高风速的带动下,不停像喷泉一样翻腾到付床上,使付床上的压力增加,床料重新返回到主床,这样就形成了高低差速床锅炉特有的内循环过程。
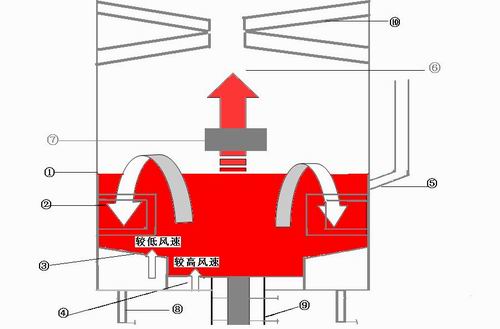
图1.1高低差速床示意图
1—水冷壁 2—埋管 3—低速床(付床) 4—高速床(主床) 5—返料 6—炉膛 7—给料口 8—风室放灰管
9—放渣管 10—凝渣管
锅炉外循环过程与常规流化床锅炉相同,只是物料的循环流较高倍率锅炉少。
内循环的意义
锅炉内循环的存在,实现了不同粒径的燃料分床燃烧的特点,使布置在付床上的埋管磨损问题得到了根本解决,同时由于主床上未布置受热面,主床上燃烧基本处于绝热状态,放出的热量除一部分由风带走外,大部分需靠内循环将其带入付床,由付床上的埋管吸收。其过程是:主床上的高温物料由内循环带入付床,与付床上的埋管受热面换热后,温度降低约50~100℃,然后重新回到主床吸热,控制主床温度。内循环使细颗粒在炉膛内循环流动,加长了停留时间,提高了燃料的燃烧效果。
六、高低差速床锅炉的特点以及原因
降低飞灰含炭量是提高锅炉热效率的关键所在。
下面,我们将分析一下影响飞灰含炭量的因素以及高低差速循环流化床锅炉是如何控制飞灰含炭量的:
炉膛内一次通过时间: 决定燃料当中的细颗粒一次性通过炉膛的时间长短,对飞灰中含炭量的影响非常大。该时间越长,燃料在炉膛内的燃烧时间越长,对降低飞灰含炭量越有利。
高低差速循环流化床锅炉宽大的炉膛,使烟气上升速度小于3m/s,加上炉膛较高的净高度,有效增加了一次通过时间,与高倍率锅炉相比,炉膛内一次通过时间是其1.5~2倍,相比之下,使飞灰含炭量大大降低。同时差速床特有的内循环,更近一步增加了细颗粒在炉膛内的停留时间,对提高燃烧效率非常有利。
2. 飞灰循环燃烧:
高低差速循环流化床锅炉的烟气分离器,对颗粒度在70μm以上的颗粒,分离效率达到95%以上,使细粉能够在炉膛内多次循环燃烧,进一步降低了飞灰当中的含炭量。
4. 合理的空气配送,保证燃烧各段所需的氧量。 高低差速循环流化床锅炉除通过主、付床输入空气外,在炉膛的稀相区设置有三次风装置,可根据燃烧情况调节三次风量,加强了稀相区氧气与燃料的均匀混合,为充分燃烧提供了有力保障。
由于密相区布设大量的埋管,成为锅炉出力强有力的保障。
宽大的炉床面积,使锅炉正常运行时,床区(密相区)蓄积了大量的高温物料,使高水份、低热值的生物质燃料被迅速烘干并燃烧干净。
高低差速床锅炉的特点,使比重不同的燃料在炉膛内均能得到有效的燃烧,质地轻的燃料首先迅速烘干并燃烧,产生纵向和横向膨胀,进入低速床,延绶高速床上较高的烟气流迅速带出炉膛,造成燃烧不完全。而质地较重的燃料可进入高速床,由高速床上较高的流速保证其正常流化燃烧。
七、存在的问题及处理措施的探讨
运行一段时间,埋管上部经常蓄集焦块,阻断了床内循环的通路,使传质传热偏离运行意愿。产生的负荷和有效周期得不到保证。
采取措施:
1、控制总风量。调试期间,我们对差速床运行时总风量一直控制为11万m³/h,主要是考虑到要强化床料流化效果,避免焦块形成。
但是运行一段时间后,密相区和炉膛出口温度均上升,锅炉出力下降。此时焦块已形成。
一旦副床上部产生焦块时,床料不能通过埋管内循环得到有效降温,相同工况下,床温升高,减少燃料供给,而埋管吸热在不断的减少,以及流化风对埋管的冷却作用,导致负荷大大降低,严重导致主床内产生焦块。
处理措施:加大所给物料的含水量,加入细粒中砂,加风,最终床内仍有焦块不断产生,负荷不断下降。最后停炉。
在稀相区,燃烧带不断上移,经常发生炉膛出口温度升高超过800度,最终导致过热器部位挂焦,填塞受热面和烟气通道,使炉膛内烟气不能及时抽出。
原因分析:我们通过试验分析总结,一是总风量的控制,二是物料配比的控制。
由于差速床锅炉吸热主要部分(约50%的负荷)依靠内循环传质传热实现,尽管存在返料设计,但在低倍速循环流化床锅炉,通过外循环返料实现传质传热不是主要的。而是通过控减总风量来强化内循环,(密相区和稀相工区徨环),达到传质传热效率,降低炉膛烟气上上升速度,提高秸秆燃烬率,主要在主床内的绝热燃烧,减少一二三次风量,尽量使风量达到或超过流化风量就可。现在运行时将总风量控制在8万m³/h以上。尽可能减少细床料,相当于中砂,在炉膛出口的杨析和夹带,减少细床料进入布袋降尘,保证密相区处于砂床状态。
2、变更生物质燃料配比。减少燃烧后碱土的产生量,因为生物质燃烧后的灰大部分为碱土,在高温时就容易形成挂渣,吸附在过热器和蓄集在埋管上方。因此采用减少软质秸秆,增加产生碱土少的生物质燃料。如大糠,硬质秸秆比例,减少产生的灰量,效果很好。(建湖公司 彭海金)
热力设备在运行期间的腐蚀与避免
热力设备在运行期间,由于所处的环境介质在特定的条件下具有侵蚀性,如不同阴离子含量、不同pH值的水等会对金属产生各种各样的腐蚀。从腐蚀形态上来说主要有均匀腐蚀和局部腐蚀,其中局部腐蚀对设备的安全运行危害较大。热力设备的腐蚀不单会缩短设备的使用年限,造成经济损失,同时还会危害到其它设备,例如,腐蚀产物随给水进入锅炉后会加剧受热面的结垢速度并进一步引起垢下腐蚀,形成恶性循环,最终造成设备事故。因此,必须采取有效措施,避免或减缓各种类型的腐蚀。
二、金属腐蚀简介
金属材料与周围的介质发生了反应而遭到破坏的现象称之为金属腐蚀。破坏的结果不但损坏了其固有的外观形态,而且也破坏了金属的物理和化学性能。腐蚀其实是一个相对概念,金属无论接触到什么介质,都会发生腐蚀,只不过腐蚀速度不同而已。
按照腐蚀机理,金属腐蚀一般可分为化学腐蚀和电化学腐蚀。
1.化学腐蚀 金属与周围介质直接发生化学反应引起的腐蚀。这种腐蚀多发生在干燥的气体或其它非电解质中。例如,在炉膛内,水冷壁外表面金属在高温烟气的作用下引起的腐蚀;在过热蒸汽管道内,金属与过热蒸汽直接作用引起的腐蚀等。
2.电化学腐蚀 金属与周围介质发生了电化学反应,在反应过程中有局部腐蚀电流产生的腐蚀。金属处在潮湿的地方或遇到水时,容易发生电化学腐蚀。这类腐蚀在生产中较为普遍,而且危害性较大。例如,钢铁与给水、锅炉水、冷却水以及湿蒸汽、潮湿的空气接触所遭到的腐蚀,都属于电化学腐蚀。
按照腐蚀的形态可分为均匀腐蚀和局部腐蚀
1.均匀腐蚀是指金属表面几乎全面遭受腐蚀。
2.局部腐蚀是指腐蚀主要集中在金属表面的某个区域,而其它区域几乎未遭到任何腐蚀的现象。局部腐蚀常见有以下几种类型:
(1)小孔腐蚀:腐蚀集中在个别点上,腐蚀向纵深发展,最终造成金属构件腐蚀穿孔。
(2)溃疡状腐蚀:在金属某些部位表面上损坏较深,腐蚀面较大的腐蚀。
(3)选择性腐蚀:在合金的金属表面上一种金属成分发生腐蚀。该腐蚀使金属的强度和韧性降低,如黄铜脱锌的腐蚀。
(4)穿晶腐蚀:腐蚀贯穿了晶粒本体,使金属产生极其细微难以察觉的裂纹。
(5)晶间腐蚀:也称苛性脆化。腐蚀沿着晶粒的边界进行,形成极为细小的交错的裂纹。这种裂纹人的眼睛无法发现,只能借助专门的仪器检查。
(6)电偶腐蚀:也称异金属接触腐蚀。两种以上的金属接触,由于各自的腐蚀电位不同,接触后形成电位差,使其中的一种金属发生快速腐蚀。例如凝汽器铜管和管板接触发生的腐蚀就属于电偶腐蚀。
与局部腐蚀的相比,均匀腐蚀金属重量损失较多,但从金属强度的损失来讲,局部腐蚀大于均匀腐蚀,尤其是发生在晶粒上的腐蚀。一般说,局部腐蚀比均匀腐蚀危害要大得多。
二、影响金属腐蚀的因素
1.水中杂质的影响尽管锅炉给水经过严格的水质净化处理,但在热力设备运行过程中少量杂质会进入水、汽循环系统,由于锅炉蒸发量很大,炉水的浓缩倍率很高,例如300MW及以上的机组,锅炉炉水的浓缩倍率一般在几十倍到几百倍。在高温、高压条件下,极易引起腐蚀。例如,我国94年规定汽包锅炉的排污率不得小于0.3%,就是避免锅炉水过分浓缩引起腐蚀问题。
2.水中溶解气体的影响 主要是水中的溶解氧和二氧化碳,其来源主要是补给水带入、凝汽器泄漏以及微量杂质在炉内分解等。这些气体溶解于水后,或影响水的pH值,或影响金属的腐蚀电位,会促进金属腐蚀。在高温、高压条件下,水的溶解氧量、电导率和pH值是影响金属腐蚀的关键因素。
3.金属所处的温度、压力以及应力等影响例如温度过高会引起金属蠕变,压力过高会使金属薄弱部位发生爆破;金属在腐蚀介质的环境中,在拉用力的作用下容易产生应力腐蚀裂开,合金钢和不锈钢尤为敏感。
三、运行期间给水系统的腐蚀及避免
(一)运行期间给水系统的腐蚀
火电厂中的给水系统包括低压给水系统和高压给水系统。其设备包括凝汽器汽侧、低压加热器、除氧器、高压加热器和省煤器以及相关的管道、阀门、泵、疏水箱等设备。由于水中溶解气体以及其它杂质的影响,在运行中给水系统的金属材料会发生溶解氧腐蚀和二氧化碳腐蚀。
1.溶解氧腐蚀
(1)原理。溶解氧腐蚀是一种电化学腐蚀,溶解氧在阴极还原和铁原子在阳极氧化而形成腐蚀原电池。在腐蚀电池中铁的电极电位比氧电极的电位低,所以铁是电池的阳极,铁发生氧化由原子变成离子而遭到腐蚀破坏。
(2)特征。钢铁发生溶氧腐蚀时,在其表面往往形成直径1~30mm的小鼓包,鼓包表层的颜色有黄褐色到砖红色,次层是黑色粉末状的腐蚀产物,去掉腐蚀产物后金属基体留有腐蚀坑。但在水流速较高的部位基本无腐蚀产物,在金属表面会出现不规则的坑洞或溃疡状的蚀面。
(3)腐蚀部位。在给水系统中,温度越低水中的溶解氧浓度越高,氧腐蚀越严重。例如,凝汽器和低压给水系统溶解氧腐蚀比较严重,其钢铁表面呈砖红色。除氧器以后的设备其表面的颜色逐渐转为钢灰色甚至黑色。一般地,从除氧器后di一个高加以后的设备不发生溶解氧腐蚀。这是因为,经除氧器去掉水中的大部分溶解氧后,剩余的少量的溶解氧在除氧器后的di一个高加已经消耗完,所以以后的设备在运行期间一般不会发生溶解氧腐蚀。但是如果除氧器运行不正常时,也可能包括省煤器甚至锅炉在内都发生溶解氧腐蚀。
2.二氧化碳腐蚀
空气中的二氧化碳约占总体积的0.03%。它溶解于水后会降低水的pH值,引起酸性腐蚀。低pH值会破坏金属表面的氧化膜,促进和加速金属的腐蚀速度。
二氧化碳腐蚀主要发生在低压给水系统。系统中二氧化碳的主要来源是补给水带入。将补给水喷淋到凝汽器中可以利用真空负压抽气系统去掉补给水中的二氧化碳和溶解氧。
(二)避免运行中给水系统金属腐蚀的方法
为了避免或减轻给水对金属材料的腐蚀,除了尽量减少进入给水中的杂质外,还应对给水进行必要的处理。目前给水处理的方法有三种。
1.还原性全挥发处理
锅炉给水加氨水和还原剂(又称除氧剂,如联氨)的处理是在物理除氧后再加氨水和除氧剂使给水呈弱碱性的还原处理。对于有铜系统的机组,兼顾了抑制铜、铁腐蚀的作用。对于无铜系统的机组,通过提高给水的pH值抑制铁腐蚀。特别适用于低压加热器含铜合金的机组。
2.氧化性全挥发处理
锅炉给水只加氨水的处理,称之为氧化性全挥发处理。
3.加氧处理
锅炉给水加氧的处理,称之为加氧处理,简称OT。采用OT可使给水系统FAC现象减轻或消除,给水的含铁量降低,省煤器和水冷壁管的结垢速率也降低,锅炉化学清洗周期延长;同时由于给水pH值的降低,可使凝结水精处理混床的运行周期延长。但是OT对水质要求严格,对于没有凝结水精处理设备或凝结水精处理运行不正常的机组,给水的氢电导率难以达到小于0.15uS/cm的要求,不宜采用OT。OT适用于低加不含铜合金,并能长期保持较好的给水水质的机组。(建湖公司 周晓芹)
|